Short Notes on the Numerical Simulation of the Effects of Oxygen Enrichment in a Turbulent, Non-Premixed, Swirling Methane-Air Burner
For many industrial processes that deal with high temperatures fuel is the main cost factor. One way to reduce fuel consumption and increase the efficiency of heat transfer to the product is by increasing the oxygen content in the oxidiser. Oxygen enrichment increases the adiabatic flame temperature, reduces the amount of transported, inert nitrogen and enhances radiative heat transfer due to an increased emission factor (higher concentrations of carbon dioxide and water) of the flue gas mixture.

Overview of the implemented geometry. Left: Air-duct (from top) and gas supply (from left), middle: swirl-generator and gas distributor, mid-right: diffusion-air spouts and burner exit into kiln-space (big brick shaped volume on the far right).
The presented simulations were done to find out how much oxygen could be added to the burner air (while maintaining the stoichiometric oxidiser/fuel ratio) to safely use existing burner technology for a high temperature kiln (up to 1750°C) used in the production of refractory bricks. The biggest risk in question was local overheating of the burner and reduced life time of the refractory bricks and high-temperature-resistant steel parts of the burner
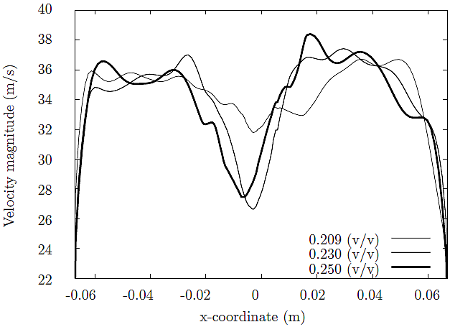
Simulation results of velocity magnitude (cell-center based values) for different oxygen concentrations in the oxidizer. Profiles are located at the diameter of the burner exit into the kiln-space.
The lowered volumetric flow rates and higher flame temperatures shift the heat transfer mechanisms from convection to radiation and potentially increase the total heat transfer rate to the product. To avoid local overheating the mixing behavior of the gases can be controlled by laminarisation. The gas mixing is slowed down in “flame-less burners” for which the radiation temperature of the flame is similar to the kiln temperature.